Encapsulated cable assemblies
Need overmolded parts that are truly custom?
You have come to the right place. IMA delivers high-quality products.
High-quality custom overmolding services for prototypes and on-demand production parts.
• On-demand molding
• Low pressure molding
• Plastic over Plastic
• Plastic over Metal
Overmolded cable assemblies are the most economical way of sealing connectors and are designed to bring performance and reliability to harsh environments.Overmolding is frequently used for:
• Low-volume production parts
• Bridge tooling
• Pilot runs
• Functional prototyping and testing
What is Cable Overmolding?
• Is highly popular because it allows pieces to be mass manufactured quickly and cheaply.
• Is a superior solution for sealing cable assemblies and connectors against rugged end-use environments.
• Is a preformed part—often metal, plastic—that is loaded into a mold where it is then overmolded with a thermoplastic resin to create a final component.
• Is a technique for layering materials on a product to offer strength, longevity, or just an aesthetic advantage.
Advantages of Overmolding
• Better product performance: Improved product performance is the main motivation to develop and manufacture a product or part utilizing overmolding.
• Shelf appeal improved: Because TPE may be utilized to produce an aesthetically appealing surface, overmolding helps a product stand out from the competition.
• Production costs are lower: Overmolding is unusual in that it increases value in multiple ways while lowering production costs. Overmolding minimizes the number of processes in the manufacturing process.
Applications of Overmolding
• Automobile Manufacturing: Insert molding is often used to make electrical sensors, gears, fasteners, and other automotive parts made of a combination of metal and plastic or rubber.
• Medicine Industry: Plastics are easier to sterilize than electrical and computer components. The medical industry relies on inserting molded and overmolded parts. Defibrillators, medical wires, and wiring are frequently enclosed in plastic via insert molding to preserve the delicate interior components while making the finished device easier to clean.
• Electrical Engineering: Insert molding a rubber exterior to electrical cables makes them safer and even waterproof in certain situations. Manufacturers commonly wrap electrical components in rubber to make goods like smartphones and computer chargers safer for users. Multiple wires are sometimes enclosed in a single sheet of rubber, while at other times, wires are separated and distinguished using contrasting colors.
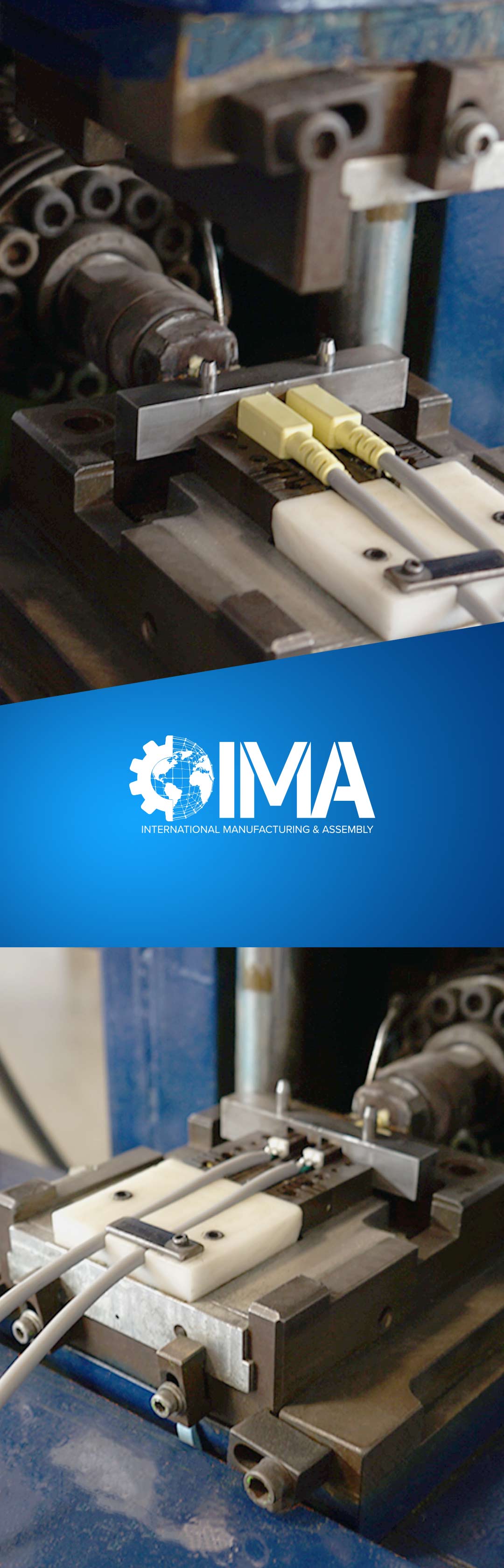
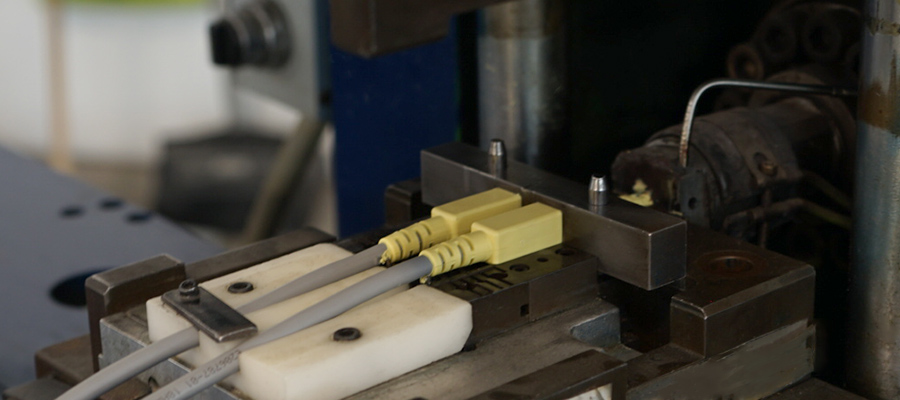
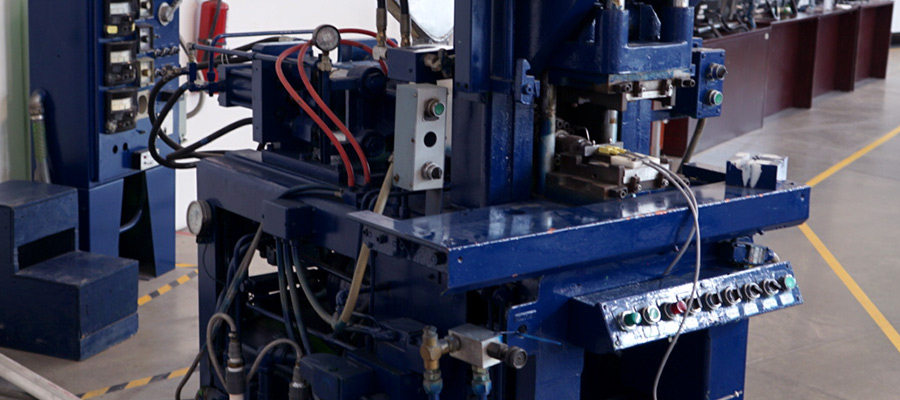
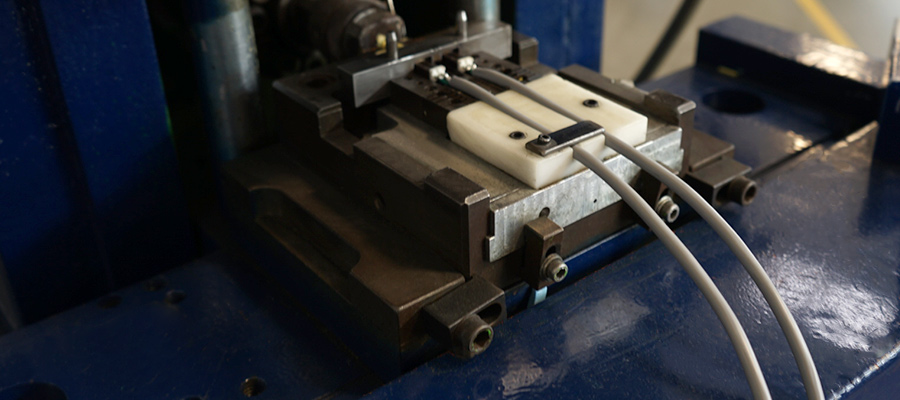
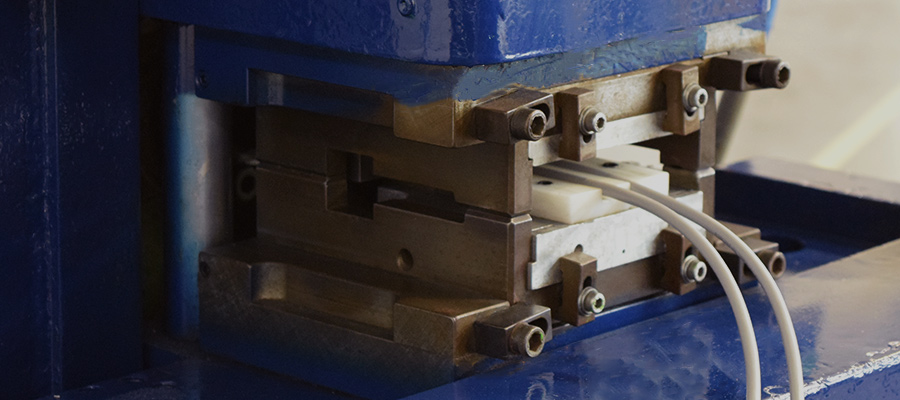