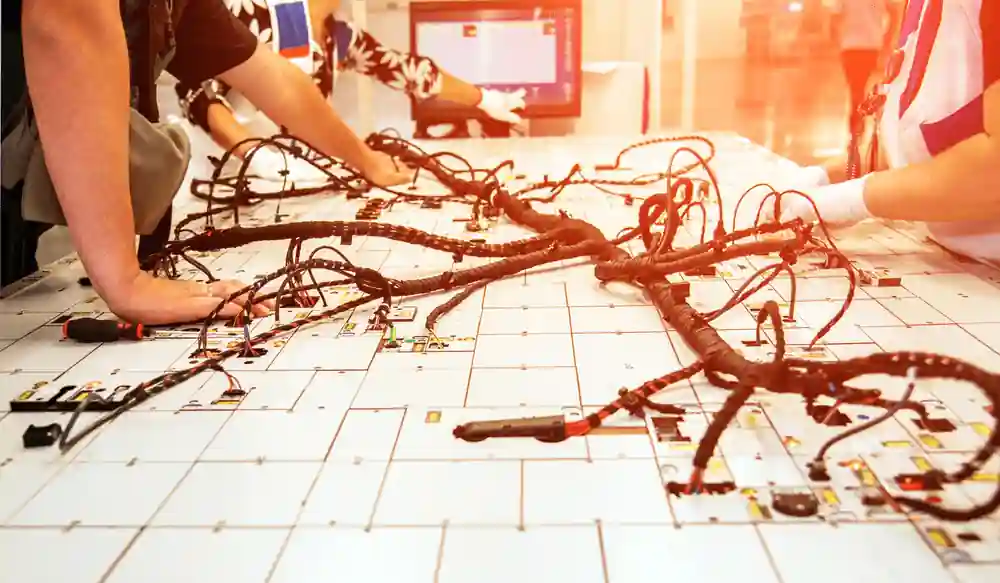
Reliable electrical connectivity is the backbone of modern industrial operations, powering everything from advanced robotics to critical medical devices. In today’s complex technological landscape, generic, off-the-shelf solutions often fall short of the demanding requirements found in specialized environments.
As a result, engineers and manufacturers increasingly turn to custom industrial cables. These specially designed cables are meticulously tailored to meet specific operational needs, ensuring unmatched efficiency, robust durability, and optimal performance where standard options simply cannot compete.
What are custom industrial cables?
Custom industrial cables are not merely electrical or data transmission cables; they are precision-engineered solutions, meticulously designed and manufactured to meet the unique and often stringent requirements of specific industrial applications. Unlike mass-produced, standard cables, these bespoke solutions are crafted with exact lengths, specialized materials, advanced shielding, precise insulation types, and custom connector configurations.
This level of customization allows these vital components to operate flawlessly and efficiently in extreme conditions, such as areas with consistently high temperatures, exposure to corrosive chemicals, environments with constant motion or repetitive flexing, or where strong electromagnetic interference could compromise data integrity.
Whether their purpose is to transmit critical power, delicate signals, or vast amounts of data, custom industrial cables guarantee a seamless and perfect fit between the cable’s design and the equipment’s rigorous operational demands, preventing performance bottlenecks and potential failures.
Benefits of custom industrial cables
Choosing custom industrial cables over standard alternatives brings a wide range of undeniable advantages, particularly in scenarios where unwavering reliability and long-term performance is absolutely critical. Some of the main benefits that drive their adoption across demanding sectors include:
- Optimized performance: Materials are meticulously tailored, and shielding is precisely engineered to significantly reduce signal loss, minimize interference from external sources, and mitigate wear and tear over extended operational periods, ensuring peak performance.
- Improved durability: Cables are specifically designed and constructed with materials chosen to thrive in their designated environments, leading to considerably longer operational lifespans and a significant reduction in costly downtime due to cable failure.
- Space efficiency: Custom lengths and precise configurations mean that unnecessary bulk or slack is entirely eliminated, allowing for more compact installations and optimized use of valuable space within complex machinery or confined areas.
- Ease of installation: With the correct connectors, precise lengths, and an optimized layout that matches the application, installation becomes significantly faster, simpler, and far less prone to errors, saving valuable time and labor costs.
- Cost control: While the initial investment for custom cables might seem higher than off-the-shelf alternatives, their superior durability, reduced maintenance needs, and extended lifespan lead to substantial long-term savings in replacement costs and operational interruptions.
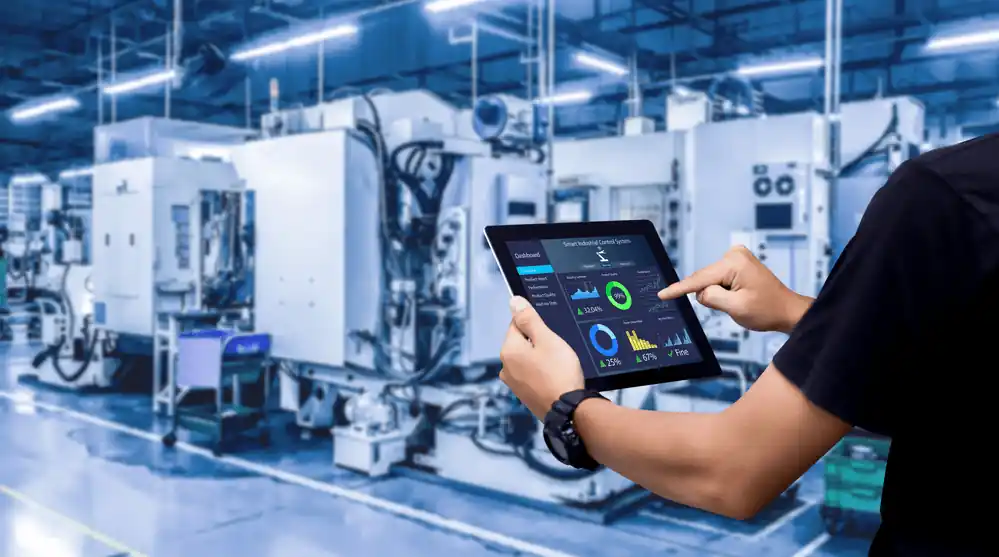
Where are custom industrial cables used?
Custom industrial cables are indispensable across a wide spectrum of industries, each presenting its own unique set of operational challenges and stringent technical requirements. Their versatility makes them the ideal choice for environments where failure is not an option. Below are some of the most common and critical environments where their specialized properties shine:
- Automation and robotics: Essential for advanced robotic arms and automated assembly lines, requiring highly flexible and rigorously shielded cables that can endure millions of cycles of continuous movement while ensuring real-time data and power control.
- Manufacturing plants: Powering heavy machinery and intricate production lines, demanding durable power and signal cables that can withstand the harsh conditions of typical factory floors, including exposure to heat, abrasion, and chemicals.
- Aerospace and defense: Critical for aircraft and defense systems, where lightweight, high-reliability cabling is paramount to withstand extreme vibrations, rapid temperature fluctuations, and often vacuum conditions, ensuring mission-critical performance.
- Medical equipment: Crucial for sensitive diagnostic tools, surgical instruments, and patient monitoring devices, requiring specialized cables that meet stringent hygiene standards, ensure biocompatibility, and deliver highly accurate signal transmission without interference.
Understanding the specific applications and environments where custom industrial cables are most effectively deployed helps decision-makers select the right design based on their unique technical demands, critical safety regulations, and desired longevity, ensuring optimal system performance and reliability.
Tailoring cables to your application
The process of designing and manufacturing custom cables involves a meticulous assessment of numerous variables. This includes voltage requirements, the specific environmental conditions (e.g., temperature range, chemical exposure, abrasion), necessary flexibility for dynamic applications, the type of signal being transmitted (analog, digital, high-speed data), and specific termination needs (types of connectors, custom pinouts).
By engaging in close collaboration with experienced cable engineers and leveraging advanced simulation tools, manufacturers can precisely design solutions that offer unparalleled long-term reliability. This iterative design process also ensures strict adherence to specific industry compliance standards, which are vital for product acceptance and safety.
Ensuring quality: The role of standards (UL, ISO, RoHS)
In the realm of custom industrial cables, adherence to established industry standards and certifications is not just a best practice, it’s a fundamental requirement for safety, reliability, and market acceptance. Organizations like Underwriters Laboratories (UL), the International Organization for Standardization (ISO), and directives such as Restriction of Hazardous Substances (RoHS) play a pivotal role in setting benchmarks. UL certifications, for instance, ensure that cables meet rigorous safety criteria against fire, electric shock, and other hazards.
ISO standards, particularly ISO 9001, emphasize robust quality management systems throughout the manufacturing process, ensuring consistency and continuous improvement. Furthermore, RoHS compliance is crucial for limiting hazardous substances, promoting environmental protection, and facilitating global market access. By conforming to these stringent standards, manufacturers of custom industrial cables provide a verifiable assurance of product integrity and operational excellence.
Ultimately, understanding the profound value of custom industrial cables is absolutely essential for any company or professional seeking optimal connectivity and sustained performance in today’s most demanding industrial environments. These specialized components not only perform with superior efficiency, but also dramatically extend the operational life of connected systems and significantly reduce overall operational costs over time.
Partnering with IMA, a leader in understanding the intricacies of every component, including specialized needs like wire harness assembly, can truly elevate your industrial applications
Recent Comments