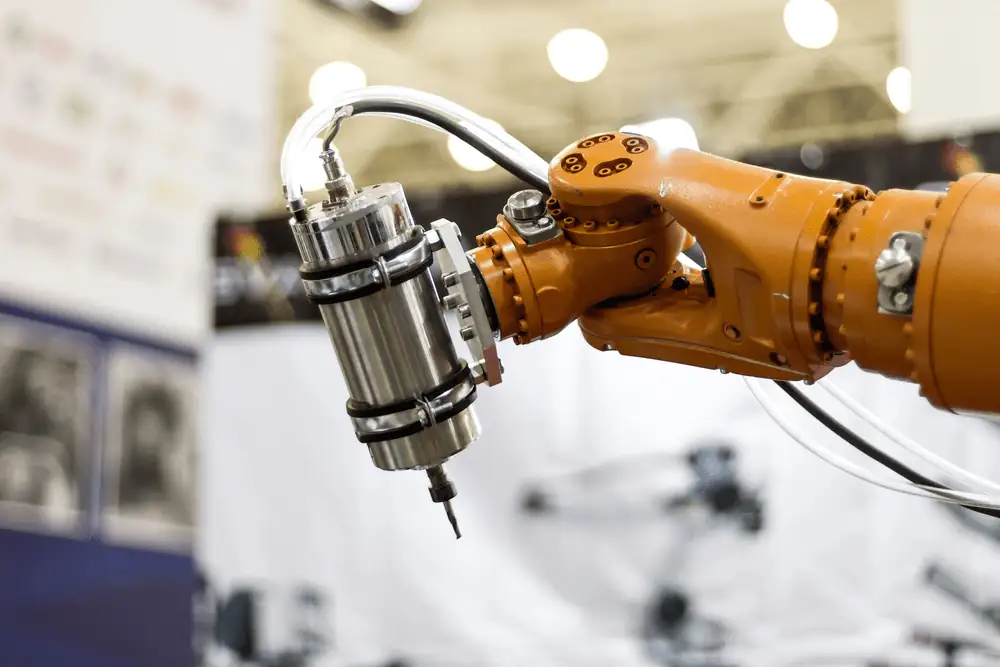
In modern manufacturing, overmolding is a widely adopted technique that plays a crucial role in enhancing product performance and usability. This process combines multiple materials into a single part to improve functionality, durability, and aesthetics. Here, we detail what is overmolding, explore its applications, and highlight its benefits across diverse industries.
What is overmolding?
To understand what is overmolding, it helps to look at it as a manufacturing process where one material is molded over another to form a unified component. Typically, a soft thermoplastic material is molded over a rigid substrate, such as metal or plastic.
This technique allows manufacturers to combine the properties of two different materials into a single product, such as adding a soft grip to a hard plastic handle or sealing electronic components with a weather-resistant layer. Overmolding improves both the function and user experience of a product.
Common applications of overmolding
Overmolding is used in a variety of industries due to its versatility and performance-enhancing qualities. Some common examples include:
- Consumer electronics: Protective layers for phone cables, USB connectors, and handheld devices.
- Automotive: Rubberized buttons, steering wheel grips, and vibration dampening components.
- Medical: Sealed instrument handles, ergonomic grips, and fluid-resistant devices.
- Industrial: Durable connectors, overmolded switches, and custom cable terminations.
Knowing what is overmolding can help product designers and engineers choose the right technique for adding durability and functionality to their components.
Benefits of overmolding
Using overmolding in product design offers a wide range of advantages:
- Enhanced durability: Protects parts from moisture, dust, and mechanical stress.
- Improved ergonomics: Provides a softer, more comfortable grip for handheld products.
- Streamlined assembly: Combines multiple parts into a single molded unit, reducing the need for adhesives or fasteners.
- Aesthetic appeal: Offers sleek, modern finishes that enhance product design.
These benefits make overmolding a go-to solution for engineers looking to improve product resilience and user experience without adding complexity.
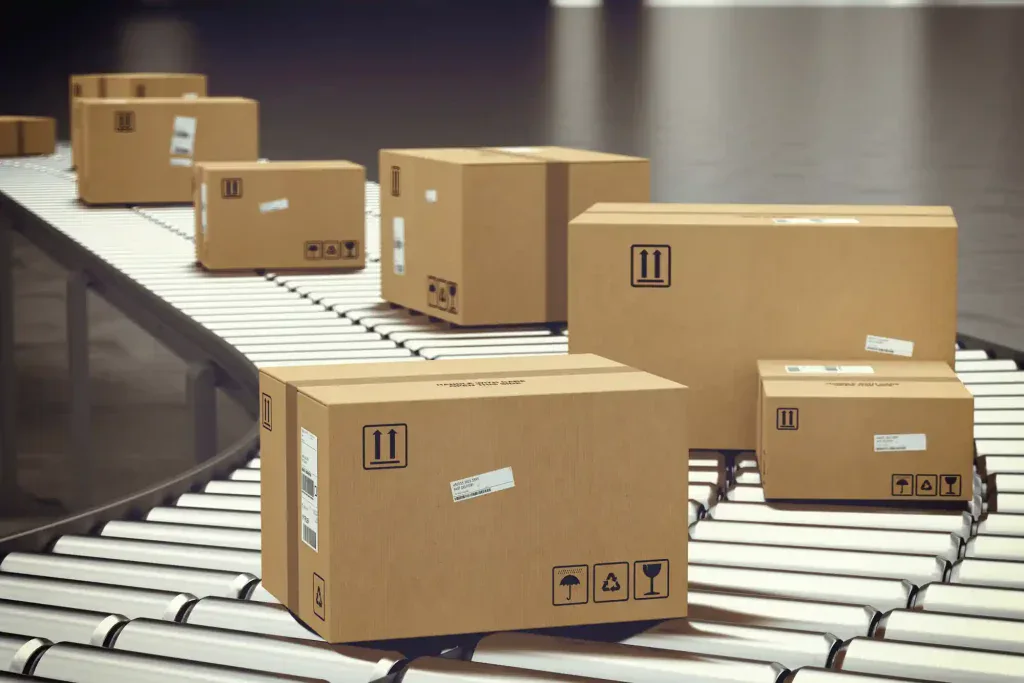
Materials used in overmolding
The overmolding process typically involves two types of materials:
- Substrate (base material): Often a rigid plastic like ABS, polycarbonate, or even metal.
- Overmold (top layer): Usually a soft thermoplastic elastomer (TPE) or thermoplastic polyurethane (TPU).
Compatibility between the materials is crucial to ensure proper adhesion and long-term performance. Understanding what is overmolding also involves knowing how material selection impacts functionality and cost.
Overmolding in scalable production
Overmolding is not only for prototyping or low-volume runs, it also scales well for mass production. Manufacturers can integrate overmolding into automated injection molding lines, reducing manual labor and improving consistency.
As products evolve and consumer expectations rise, overmolding remains a practical solution to meet both technical and aesthetic demands at scale.
Design considerations and limitations
While overmolding offers many advantages, there are important considerations:
- Tooling cost: Initial mold design can be more expensive compared to single-material parts.
- Material compatibility: Not all materials bond well; testing is often required.
- Cycle time: Overmolding involves multiple molding steps, which may affect production speed.
Being aware of these factors ensures that overmolding is used effectively and cost-efficiently in your project.The overmolding technique provides unparalleled advantages in enhancing product design, durability, and functionality. By effectively safeguarding critical components, such as wire harness assemblies, overmolding enhances their protection and resilience. This not only boosts the longevity and reliability of components but also optimizes overall product performance. At IMA, our focus is on high-quality wire harness assembly, that’s why we recognize how overmolding can complement and enhance these components, ensuring they integrate seamlessly into your advanced manufacturing solutions.
Recent Comments